What is capacity planning? Defined by example
- 22 Nov, 2022
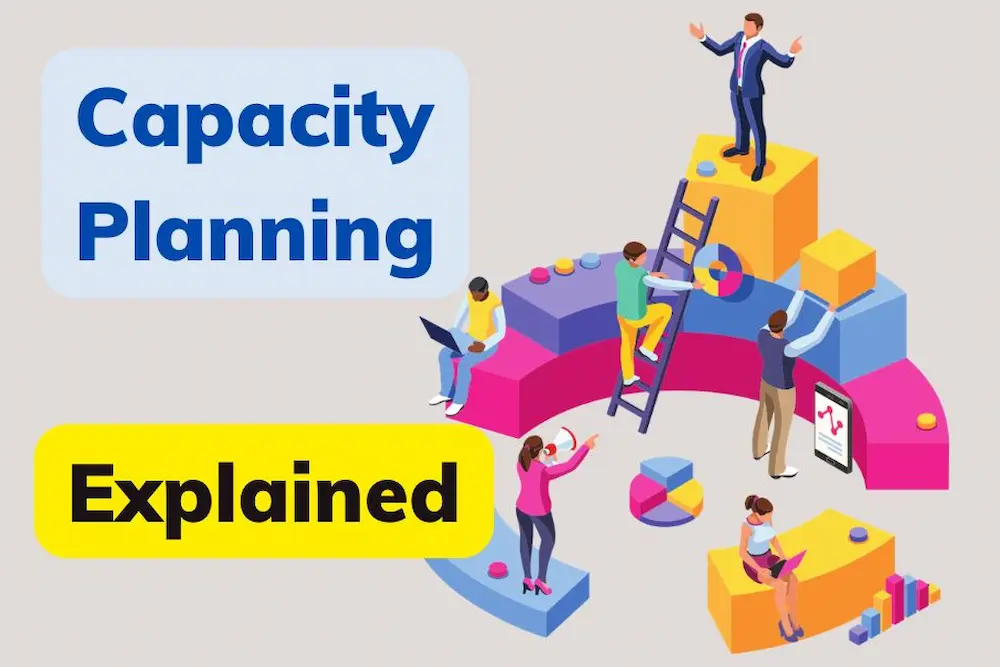
Planning is thinking about the activities required to achieve the desired goal. It is based on prediction and estimation based on past experiences, data, and current conditions. Plans help teams stay on track and march toward the shared objective.
So it’s not a surprise that we are pro-planning, as is everyone with a business to run. But what is capacity planning? Simply put, capacity planning estimates the resources required to deliver a specific product in a given period. Things like how many workers would be needed, how many hours would be required etc.
It’s not an exact science. It’s not perfect, but the results can get pretty close with advanced technology and data. Businesses can get a rough framework to start a project. Their margin of error and mismanagement steeply declines with capacity planning as opposed to working in complete darkness, and your team has a rough blueprint for planning further.
Let’s understand capacity planning and its benefits in further detail with some great examples:
What is Capacity Planning?
Understanding and predicting the production capacity of a business is the crux of capacity planning. A ton of variable factors affect the production capacity of your business; capacity planning is the science of taking these changing factors into account and coming up with a workable plan to meet consumer demands.
It’s all about balancing available resources and the demands of the project or client. One must have heard the term capacity in reference to production ability.
For example:
-
A company has 10 employees.
-
Each employee works 50 hours/per week.
-
50 x 10 = 500 hrs
-
The company has 500 hrs of weekly capacity.
This company can take care of a maximum of 500 hours of business each week.
Capacity planning helps in:
-
Resource management
-
Time management
-
Team management
-
Work management.
It’s essential to understand the importance of capacity planning in project planning. Every business will have a different approach in how they carry out planning depending on the unique demands and challenges that their business faces. Various capacity planning strategies can be employed in different situations:
Capacity planning strategies
Capacity planning has no one shoe fits all answer. Depending on the situation, a different strategic and planning approach is adopted. There are three primary capacity planning strategies extensively used by managers:
- Lead strategy
Taking action in advance to increase your capacity to meet future demands is the core idea of the lead strategy. In this aggressive capacity planning approach, businesses increase their capacity in anticipation of demand increasing in the future.
An example of a lead capacity planning strategy would be buying a bigger warehouse or stocking up on raw materials in bulk for the following year.
The lead method is widely employed to increase market share and profit from rivals that frequently have inventory shortages, particularly during peak demand seasons. However, this technique risks producing excess inventory and greater stock-holding costs if the anticipated demand does not match the actual demand.
- Lag strategy
As you must have guessed from the name, lag strategy is the opposite of leadership strategy. It involves waiting till the current capacity is stretched to its limit to increase your capacity.
This reactive strategy benefits small businesses that want to avoid high holding costs. However, this strategy can cost you brief delays as it’s not always possible to meet the capacity demands at the last minute.
- Match strategy
Match strategy is the middle ground between the lead and lag capacity planning approaches. It doesn’t boost capacity in advance nor wait for demands to get out of hand; it gradually increases the company’s capacity.
These adjustments are based on the most recent market conditions, necessitating that companies regularly monitor capacity use and, as needed, meet demand in increments. Although this technique requires more intricate effort, it is often safer for businesses because it is proactive and risk-averse.
What is the Capacity Planning Process?
Now that you know what capacity planning is and what different strategies you can use, let’s understand how the capacity planning process works:
- Measure
Data is very important in ensuring that your planning process is accurate. You must measure the time and resources that go into finishing a project. Measuring this data would help you plan better.
For example,
You have 5 projects, each requiring 200 hours per week.
5 x 200 = 1000.
That means your total product demand is 800hrs/ week.
You have 20 employees working 50 hours per week at a utilization rate of 80%.
20 x 50 x 0.8 = 800
This makes your work capacity 800hrs.
1000 - 800 = 200hrs.
This means you have 200 hours of work per week that needs to be allotted.
- Analyze
Once you start measuring your capacity, you can make proper decisions based on the numbers.
You have an extra 200 hours of work and need more resources to do it. So you need to decide here whether you want to hire another employee or assess the profitability of the projects you have taken on.
- Track
Tracking your resources is a crucial part of the planning process.
You can start tracking the time your employees spend on each project and then analyze whether it’s time to renegotiate the billing rates with the client if you find that a specific project consumes more time than you first anticipated.
You can create more precise capacity plans in the future using time-tracking data.
The example we used above is the oversimplification of the process; in reality, there is a slew of different factors and resources that need to be considered to get effective results.
Conclusion
Capacity planning enables businesses to deliver on the demands of their clients. This strategic planning may be incorporated into daily operations to help businesses meet deadlines, efficiently grow production, and boost profits.